A Safer, Eco-Friendly Polymer for Implantable Medical Devices
An innovative polymer, PHOx, could significantly improve the safety of implantable medical devices while also being more environmentally friendly.
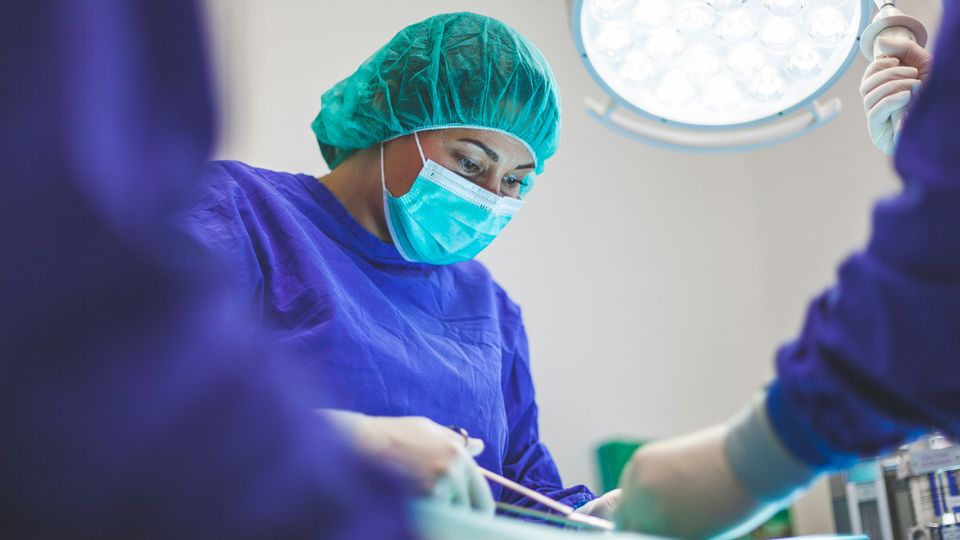
Complete the form below to unlock access to ALL audio articles.
Every year, millions of patients receive medical devices inserted or implanted in the cardiovascular system: arterial and venous catheters, cardiac devices, pacemaker leads, artificial hearts, vascular prostheses, etc. These devices, often made from polyurethane (PU), perform vital functions, but are not without defects. PU production relies on toxic chemicals called isocyanates, and PU is also partly responsible for serious complications in patients, such as blood clots and infections.
Faced with these limitations, a team from the GIGA (Cardiology Laboratory) and the CESAM (Centre de recherche sur les macromolécules - CERM) at the University of Liège has come up with a promising alternative: PHOx, a thermoplastic elastomer without isocyanate PU (NIPU), which is therefore less toxic to produce and much better tolerated by the human body.
"PHOx (Poly Hydroxy-Oxazolidone) is a flexible, transformable plastic that can be moulded, pressed, spun into fibres or 3D printed," explain Anna Pierrard, chemist, and Christine Jérôme, Director of CERM. It can thus be used to produce a variety of personalised medical devices. Better still, its manufacture is based on 'greener' raw materials, derived in particular from carbon dioxide, reducing the environmental impact of the process.
"Extensive laboratory tests have shown that PHOx outperforms PU in several key respects," enthuse Sofia Melo, bioengineer, and Cécile Oury, FNRS Research Director and Head of the Cardiology Laboratory at the GIGA. PHOx is more compatible with blood. In particular, it reduces the adhesion of platelets (essential cells in the formation of blood clots) and the activation of coagulation, limiting the risks of clot formation. It is also thought to inhibit the adhesion of bacteria such as staphylococcus aureus, which is often implicated in implant infections. No toxicity was observed, either for human cells or during implantation, and the material did not cause excessive inflammation, degradation or rejection.
3D printable implants
Another major advantage of PHOx is that it can be easily 3D printed. "This means that we could eventually produce custom-made devices for each patient, reducing waste and at lower cost," explains Patrizio Lancellotti, Head of Cardiology at Liège University Hospital." Tailor-made implants, heart valves adapted to the anatomy of each individual: the applications are numerous.
Thanks to its mechanical (flexibility, strength) and biological (biocompatibility, compatibility with blood, stability) properties, PHOx could well replace PUs in many medical applications. This is a major step towards medical devices that are safer for patients, more environmentally friendly, and potentially more economical thanks to customised manufacturing and reduced healthcare costs associated with fewer complications.
The researchers stress that this is the first time that a NIPU (non-isocyanate polyurethane) material has demonstrated such performance in critical medical applications.
This major advance has been published in the scientific journal Advanced Healthcare Materials, and an international patent application (WO2025082761) has already been filed.
Reference: Melo SF, Pierrard A, Lifrange F, et al. Poly(Hydroxy‐oxazolidone) thermoplastic elastomers for safer, greener and customizable blood‐contacting medical devices. Adv Healthc Mater. 2025. doi: 10.1002/adhm.202502670
This article has been republished from the following materials. Note: material may have been edited for length and content. For further information, please contact the cited source. Our press release publishing policy can be accessed here.