Analytical Action To Ensure Water Availability in Semiconductor Manufacturing
Whitepaper
Published: June 17, 2025
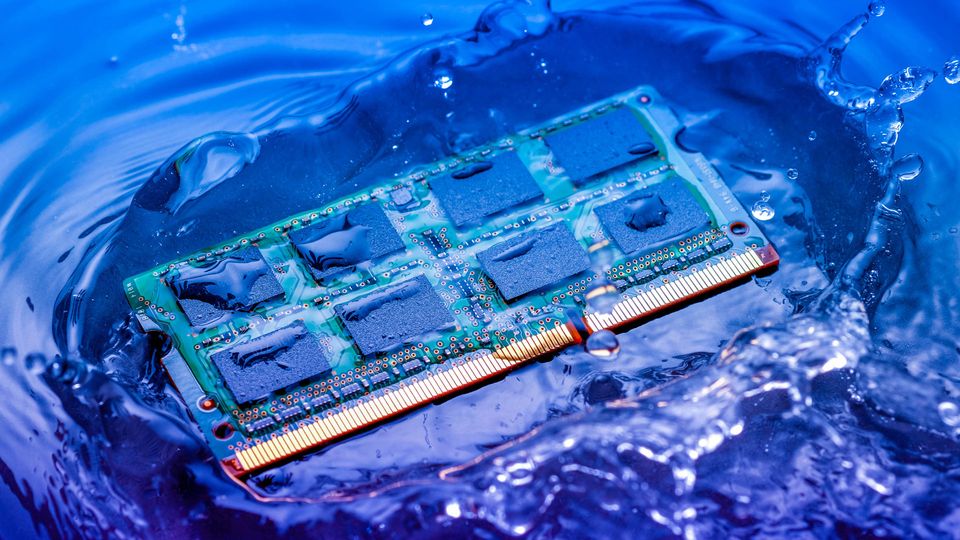
Credit: PerkinElmer
Amongst growing demand for semiconductors, and the water usage required for their manufacture, there is an increasing need for stringent contaminant monitoring in water recycling operations.
Inductively coupled plasma mass spectrometry (ICP-MS) users are embracing multi-quadrupole technology, which has several features to enhance analytical performance for measuring contaminants in ultrapure water.
This whitepaper examines innovations in water usage and recycling within the semiconductor industry, exploring the analytical challenges in elemental contamination monitoring.
Download this whitepaper to discover:
- Why water purity matters in semiconductor manufacturing
- Process considerations for elemental impurity analysis in water recycling
- How the latest ICP-MS innovations enhance sensitivity to detect ultra-trace level contaminants
WHITE
PAPER
Semiconductor Water Recycling:
Analytical Action to Ensure Consistent Water Availability
Introduction
As the demand for semiconductors increases, Fabs will rely on higher quantities of water for
processing. Semiconductor manufacturing utilizes an incredible amount of water, for instance,
a single 200-mm or 8-inch wafer can require over 5,600 liters or 2,000 gallons of water.1 Water
usage is also being driven by the need for more complex semiconductors, as the more layers
used to manufacture these complex wafers, the more washes are needed to process them.1 Thus,
more advanced logic circuits will require even more water to manufacture compared to past
semiconductors.
Changing climate conditions are increasing temperatures, leading to more frequent drought
conditions. Draught formation is exacerbating an already strained water allocation issue
for semiconductor companies. For example, Taiwan is experiencing water issues in Tainan,
Kaohsiung, Taichung, and Hsinchu.1 The United States has decided to increase its semiconductor
manufacturing and has several major semiconductors companies, such as TSMC and Intel,
building Fabs in Arizona.1 The dry, arid conditions of Arizona and the limited water sources
available will require US manufacturers to place an added emphasis on water allocation strategies.
The Fabs that do have favorable access to water sources still must consider the environmental
toll of substantial water resource removal for semiconductor processing. The balance of heavy
water usage between agriculture and semiconductor manufacturing adds further strain on the
water availability for these Fabs.1 Thus, water recycling is a critical factor in the viability of longterm
semiconductor manufacturing. This whitepaper will examine the trends and innovations in
water usage and recycling within the semiconductor industry.
Water Usage Demand Increases in Semiconductor Applications.Semiconductor usage continues
to grow in a number of consumer, commercial, and industrial products. This expansion is
projected to increase in the future along with the complexity of the chips.2
Some of the applications of semiconductors include:
Personal electronic devices such as computers and tablets, mobile phones, and smartwatches2
Household items such as televisions, appliances, LED light bulbs, and heating/cooling equipment2
Commercial and industrial products such as lasers, optical sensors, solar batteries, medical
diagnostic equipment, traffic lights, and industrial machinery2
Semiconductor Water Recycling: Analytical Action to Ensure Consistent Water Availability
www.perkinelmer.com 2
Semiconductor Production
Semiconductor production has a design and fabrication phase,
where companies that focus solely on design are known as
fabless firms and companies that focus only on fabrication are
called foundries. Companies that do both the design and the
fabrication are called Integrated Device Manufacturers (IDMs).2
An overview of the semiconductor production process includes:
Silicon extraction
from raw material
Purification
Cylindrical ingot
formation, from
one to nearly 18
inches (450 mm) in
diameter, up to 200
pounds each
Semiconductor
design
Process engineering
Raw and fabrication
materials selection
Quality control (QC)
program design
Ingots are sliced into
1 mm-thick discs or
“blank wafers”
Wafer diameter is
adjusted if needed
Multiple layers of
transistors and wiring
are formed on the
wafer surface in an
iterative process
Steps include
cleaning, oxidationdiffusion,
deposition,
photoresist
patterning, etching,
ion implantation
Wafer is cut
into individual
semiconductor units
called dies
Semiconductor chip
packaging
Each finished chip
is attached to and
encased in protective
housing
Raw Material
Processing
Research and
Development (R&D)
Blank Wafer
Production Wafer Processing Wafer Cutting
Cleaning
Oxidation and Diffusion
Deposition
Photoresist Patterning
Inspection and Metrology
Etching
Ion Implantation
Figure 1. Steps of the circuit information process are repeated to build a multi-layered IC.
These key steps are composed of 400 to 600 detailed steps that
are typically completed over one to two months. Figure 1 outlines
the steps of the circuit formation process that are repeated to
manufacture a multi-layered integrated circuits.
Semiconductor Water Processing and Contaminants
The majority of water used in semiconductor manufacturing
is used in washing and wet cleaning steps, where ultrapure
water is utilized. Raw water sources are brought into a variety of
processing steps to achieve ultrapure filtration. The processing
of raw water removes contaminants that can affect the wafer’s
functionality. As semiconductor’s become more efficient
at smaller scales, they will also become more vulnerable to
interferences via chemical and particulate contaminants.2
Therefore, manufacturers need technological support to detect
ultra-trace levels of contaminants through the fabricating
process. As the industry continues to trend to smaller and
more advanced semiconductor products, detecting chemical
contaminants at the parts per trillion (ppt) level is no longer
adequate, with levels as low as parts per quadrillion (ppq)
detection limits needing to be analyzed.1,2
As wafer complexity increases for more complex performance,
the number of layers will increase in manufacturing. Each layer
requires water washing during processing, thus the more layers
there are the more ultrapure water will be needed.2
Semiconductor Water Recycling: Analytical Action to Ensure Consistent Water Availability
www.perkinelmer.com 3
Treating Wastewater
The immense water utilization steps of semiconductor
manufacturing generate a lot of wastewater, which typically
requires post-utilization treatment.3 The diversity of wastewater
created, which is dependent on the specific application of
manufacturing, requires different treatment protocols that utilize
technologies that range in cost. For example, UV light is relatively
cheap on an industrial scale while other treatments, such as
reverse electrodialysis, are much more costly. Large foundries
separate the streams and each wastewater stream has its own
specific treatment depending on the chemicals and contaminants
collected during manufacturing. Of this treated water output, a
portion is reusable and can be put back into the system to generate
more ultrapure water.3 The water that is not reusable is often stored
in cooling towers where it is used to help maintain temperatures.3
Semiconductor manufacturing process wastes can generate a
variety of wastewater streams and the stream’s contaminant
profile is dependent on the materials and processes being used
at that particular facility.3 Analytical assessment of discharged
process wastewater must be subject to periodic sampling and
analysis prior to its transfer to a treatment facility.3 Therefore, the
characterization, storage, and transport of this waste must adhere
to requirements set forth by local, state, and federal authorities.3 The
waste treatment and disposal facilities require analytical data on the
content of each unique waste stream to ensure compliance.
Figure 2 shows the semiconductor water production overview.
Water Recycling
Due to the complexity and price of implementation of water
recycling capabilities, smaller semiconductor companies have
been slower to adopt its use. However, Large FABS, such as
TSMC, Samsung, and Intel, must implement these water reuse
and recycling technologies due to their large water requirements.3
In 2019, TSMC fabs in Tainan alone consumed 50,000 metric
tons or 50 million liters of water per day.3 Sourcing this amount
of water is not only an industrial challenge but an environmental
obstacle as well. The Nanhua and Zengwen reservoirs are where
the TSMC fabs were drawing water from, and their capacity
dropped to significantly low levels.3 This environmental challenge
is exacerbated further as Southern Taiwan is also its agricultural
region and primary food developer.3 In order to continue extracting
water, fabs have had to enhance their water draw and usage
capabilities in the form of water recycling optimization and
rainwater collection systems.3 Additionally, fabs are placing
added environmental protection procedures that utilize advanced
filtrations systems including:
Reverse osmosis filtration
Hollow fiber ultra-filtration
Sand filtration
Feed
Water
RO
Blend Water
Water
Product
Water
Reclaim
Tank
Facilities
Operations Wastewater
Treatment
Semiconductor Factory (Fab)
Incoming
Raw
Water
Non-UPW Process Water
UPW Recycle
Central Scrubbers,
Cooling Towers,
Irrigation
Evaporation
(Cooling
Towers)
Sanitary
Wastewater To Final Outfall
Wastewater
Fab Recycle Water
Reclaim Water
Wastewater
Irrigation
Portable Water
UPW Plant
POU Scrubbers,
Humidification
UPW Supply
UPW Return
Figure 2. Semiconductor water production overview.
Semiconductor Water Recycling: Analytical Action to Ensure Consistent Water Availability
www.perkinelmer.com 4
Why Water Purity Matters
Ultrapure water (UPW) is critical in the production of
semiconductor devices as it is utilized in most of the wet
processing steps, including wafer-rinsing and the dilution of
compounds used in chemical baths. During wet processing,
contaminants from the chemical baths and the rinsing water
waste can be adsorbed and precipitated onto the silicon surface
via several chemical and electrochemical reactions.3
The nano-metallic particles present in the critical areas of the
finished product can change the electrical parameters of the
components of an integrated circuit, leading to failed electrical
tests.3 If particles land on the photoresist during the lithography
phase a projection error can occur on the wafer.3 Additionally,
contamination can contribute to static shocks that can affect
the wafer’s design.3 All of the damages resulting from these
contaminants impact wafer yield and production efficiency.
Thus, water purity is critical in semiconductor processing to
mitigate contamination exposure to the wafer and electrical
short-circuiting.
Impurities are classified into the following categories:
Particles
Bacteria
Total Organic Carbons
Silica
Metals and Ions
Gases
Purity Standards
The purity standards for ultrapure water have dramatically
over the last two decades. Today, the standards are even
more stringent and as the standards continue to tighten up
on contamination levels, ultrapure water processing will need
to rely on advanced analytical and filtration technologies.
Semiconductor Equipment and Materials International
(SEMI) and the American Society for Testing and Materials
International (ASTM International) have demonstrated
increasingly more stringent standards in ultrapure water
analysis. In SEMI F63-0918 "Guide for Ultrapure Water used
in semiconductor processing”, the target values for 26
metallic contaminants are less than
1 ppt with the exception of boron (50 ppt) and nickel (3 ppt).4
The reported method detection limits (MDLs), show values of
0.5 ppt for all elements, with the exception of born (15 ppt)
and nickel (1.6 ppt).4 Inductively coupled plasma mass
spectrometry (ICP-MS) is the only technology that can
accurately determine this collection of elements at such
low levels and in a short period of time.
Elemental Impurity Analysis with ICP-MS
With the addition of increasingly stringent contaminant
monitoring in semiconductor water recycling operations,
ICP-MS systems are embracing multi-quadrupole technology
with triple quadruple technology, i.e., PerkinElmer’s
NexION 5000.
Novel Triple Cone Interface (TCI) with OmniRing™ technology
provides outstanding sensitivity
Plasma Generator
The balanced and free-running RF generator design delivers
improved robustness, high efficiency, wide power range
and ensures fast power-switching between Cold and Hot
Plasma modes.
LumiCoil™ RF coil is passively cooled by the extraction
(not requiring water or gas cooling), so is maintenance-free,
eliminating the need to replace plasma load coils
Multi-Mode Methods
Takes advantage of these technologies in combination
with a cell-based Reaction mode (in the Universal Cell) and
multi-quadrupole technology, yielding superior polyatomic
interference removal that can further improve detection limits
(DLs) and background equivalent concentrations (BECs).
Quadrupole Universal Cell
Unlike passive cells, such as octopoles and hexapoles, the
Universal Cell is a quadrupole; therefore, it has the ability to
control the reaction chemistry through the implementation
of the rejection parameter “q”. This parameter is able to
prevent byproducts of the original reaction from forming
new interferences with any water vapor residues or cell
gas impurities which may have been introduced into the
cell.
Four Gas Channel Configuration
With four gas channels available, up to four gases can be
used in the same method, delivering ultimate flexibility in
the removal of any particular interference.
The following ICP-MS considerations are designed to enhance analytical performance, sensitivity of the instrument, and reliability:
Semiconductor Water Recycling: Analytical Action to Ensure Consistent Water Availability
www.perkinelmer.com 5
Multi quadrupole technology makes interference removal by
chemical reactions and Mass Shift mode even more effective
since the first transmission quadrupole (Q1) set at
< 0.7 amu resolution does not allow other species than those
at the analyte mass to be transmitted further. This operation
effectively cleans the ion beam and the background before it
enters the cell. The Universal Cell (Q2), via gas reactions, deals
with spectral interferences and then the analyzing quadrupole
(Q3), also set at < 0.7 amu resolution, rejects products other
than an analyte of interest.4
Scans shown in Figures 3 and 4 explain in detail how Reaction
mode with multi-quadrupole technology works. In Figure 2, there
is a Q3 scan (Single Quad mode) of a 100 ppt multi-element
standard from mass 75 to 92 while O2 was introduced into the
Universal Cell. The Q1 quadrupole acts as an ion guide
transmitting all masses. The analyzed standard is a mixture of
50 elements including Ge, Zr and diluted HCl. Multiple peaks
from the components of this standard are displayed and a
peak formed by AsO+ is present at mass 91.4
The same mixed-element standard solution was scanned in
Product Ion Scan mode with O2 (Figure 4), with Q1 set to 0.7
amu resolution at mass 75 instead of transmitting all ions.
The plot shows a clean background with only two peaks -
Co0+ and ArCl- at mass 75 and as seen as AsO- at mass 91.
Consequently, arsenic is measured in the Mass Shift mode
after the reaction with O2 without having to worry about
potential interferences from Ge, Zr, and Cl.4
Figure 3. Q3 scan (Single Quad) of a 100-pt mixed-element standard from mass 75 to 92.
Figure 4. MS/MS scan of a 100-ppt mixed element standard from mass 75 to 92 while Q1 transmits only ions at mass 75.
P
u
l
s
e
I
n
t
e
n
s
i
t
y
P
u
l
s
e
I
n
t
e
n
s
i
t
y
Semiconductor Water Recycling: Analytical Action to Ensure Consistent Water Availability
www.perkinelmer.com 6
Using MS/MS and Mass Shift modes with reaction gases
(Reaction mode) and without reaction gases (Standard mode),
DLs and BECs were measured for 50 elements in ultrapure
water. This analysis used hot plasma conditions and a onesecond
integration time per isotope.4
Table 1 shows the results of 26 semiconductor-essential
elements. Detection limits in Hot Plasma mode for all 26
essential elements for the semiconductor industry were found
to have concentrations lower than 0.3 ppt, easily fulfilling
the 1-ppt requirement by SEMI or ASTM standards. BECs
for most of the elements were found to be less than 0.5 ppt,
demonstrating the effectiveness of the gas reactions and
the MS/MS modes in removing spectral interferences.4
In Table 2, DLs and BECs for an additional 24 elements are
shown with similarly low values for both parameters. For
the BEC and DL measurements, calibration curves were
established with 10, 20, 40, and 60 ppt standards. All curves
had linear regression values (r2)> 0.999, demonstrating the
linearity of the analysis, the ability to accurately measure
at low concentrations, and the effectiveness of the
interference removal.4
Element Mode
Isotope
Selection
(Q1/Q3)
DLs BECs
Li Standard 7/7 0.028 0.018
B Standard 11/11 0.178 0.239
Na Standard 23/23 0.091 0.108
Mg Standard 24/24 0.028 0.026
Al Reaction Ammonia 27/27 0.049 0.180
K Reaction Ammonia 39/39 0.158 0.459
Ca Reaction Ammonia 40/40 0.085 0.412
Ti Reaction Oxygen 48/64 0.033 0.007
V Reaction Ammonia 51/51 0.009 0.004
Cr Reaction Ammonia 52/52 0.081 0.340
Mn Reaction Ammonia 55/55 0.055 0.015
Fe Reaction Ammonia 56/56 0.173 0.915
Co Reaction Ammonia 59/59 0.017 0.026
Ni Reaction Ammonia 60/60 0.271 0.433
Cu Reaction Ammonia 63/63 0.030 0.081
Zn Reaction Ammonia 66/66 0.085 0.126
As Reaction Oxygen 75/91 0.109 0.045
Sr Standard 88/88 0.007 0.008
Mo Reaction Ammonia 98/98 0.038 0.033
Cd Standard 114/114 0.058 0.027
Sn Standard 118/118 0.075 0.012
Sb Standard 121/121 0.050 0.077
Ba Standard 138/138 0.014 0.012
W Standard 184/184 0.053 0.042
Pt Standard 195/195 0.268 0.271
Pb Standard 208/208 0.031 0.014
Table 1. UPW DLs and BECs in ppt for 26 essential elements for the semiconductor
industry measured in Hot Plasma mode.
Element Mode
Isotope
Selection
(Q1/Q3)
DLs BECs
Be Standard 9/9 0.116 0.060
Si Reaction
Hydrogen+Ammonia 28/28 25.9 446.8
P Reaction Oxygen 31/47 2.86 1.39
S Reaction Oxygen 32/48 8.7 195.1
Sc Reaction Oxygen 45/61 0.022 0.008
Ga Standard 69/69 0.014 0.007
Ge Reaction Ammonia 74/74 0.071 0.294
Se Reaction Oxygen 78/94 1.160 0.652
Nb Standard 93/93 0.015 0.012
Ru Standard 102/102 0.040 0.097
Rh Standard 103/103 0.162 0.073
Pd Standard 106/106 0.055 0.033
Ag Standard 107/107 0.107 0.064
In Standard 115/115 0.014 0.008
Te Standard 130/130 0.057 0.070
Hf Standard 180/180 0.017 0.025
Ta Standard 181/181 0.006 0.010
Re Standard 187/187 0.045 0.017
Ir Standard 193/193 0.047 0.587
Au Standard 197/197 0.062 0.103
Tl Standard 205/205 0.017 0.007
Bi Standard 209/209 0.004 0.011
Th Standard 232/232 0.028 0.016
U Standard 238/238 0.016 0.019
Table 2.UPW DLs and BECs in ppt for non-essential elements for the semiconductor
industry measured in Hot Plasma mode.
Semiconductor Water Recycling: Analytical Action to Ensure Consistent Water Availability
For a complete listing of our global offices, visit www.perkinelmer.com/ContactUs
Copyright ©2024, PerkinElmer U.S. LLC. All rights reserved. PerkinElmer® is a registered trademark of PerkinElmer U.S. LLC. All other trademarks are the property of their respective owners.
105079
PerkinElmer U.S. LLC
710 Bridgeport Ave.
Shelton, CT 06484-4794 USA
(+1) 855-726-9377
www.perkinelmer.com
Cold Plasma mode, in conjunction with MS/MS, is able to obtain
extremely low DLs and BECs in Standard and Reaction (NH3)
modes for a few elements that have Ar-based interferences or
whose sensitivity is enhanced by the reduction of Ar ions in the
plasma stream as outlined in Table 3.4
Thus, advanced multi-quadrupole ICP-MS systems, such as
the NexION 5000, that contain optimized sample introduction
systems, load coils, 34-MHz RF plasma generators, and a
universal cell with four gases should be a key consideration in
semiconductor processing facilities.
The Future of Water Recycling in Semiconductor Manufacturing
Increased semiconductor demand in both volume and
complexity and global warming trends will continue to expand
the amount of water recycling necessary to remain viable in the
semiconductor industry. To compound this issue further, water
recycling operations will face more stringent standards and will
require the use of advanced analytical technologies to meet
these expectations.
By utilizing the latest innovations in ICP-MS technology,
manufacturers can leverage the most sensitive and robust
analytical systems to meet these standards and optimize their
water recycling strategies. Those that adapt to this evolving
semiconductor landscape by incorporating these analytical
systems and rise to this water challenge will not only ensure
their viability but will help ensure the industry moves in a more
sustainable direction.
References
1. The Big Semiconductor Water Problem. 2022. Asianometry.
https://www.asianometry.com/p/the-big-semiconductorwater-
problem#:~:text=It%20takes%20about%206%2C000%20
liters%20or%201%2C600%20gallons,5%2C600%20liters%20
or%202%2C000%20gallons%20of%20ultrapure%20water.
2. Semiconductor Whitepaper. PerkinElmer. 2020. https://pki.
showpad.biz/webapp2/content/channels/ad1090a5ba40efa83
71b8625f5573852/682b82d11146d770a900d495ff630daa577
b68be8621659a82a719bb8c55928/f682b82d11146d770a900d
495ff630daecf4165fa73c55ede52e77401b0ea5ae?page=5.
Element Mode
Isotope
Selection
(Q1/Q3)
DLs BECs
Li Standard Cold 7/7 0.0004 0.0001
Na Standard Cold 23/23 0.033 0.045
Mg Standard Cold 24/24 0.008 0.004
Al Reaction Cold
Ammonia 27/27 0.012 0.005
K Reaction Cold
Ammonia 39/39 0.030 0.021
Ca Reaction Cold
Ammonia 40/40 0.025 0.050
Cr Reaction Cold
Ammonia 52/52 0.011 0.020
Mn Reaction Cold
Ammonia 55/55 0.006 0.003
Fe Reaction Cold
Ammonia 56/56 0.009 0.052
Co Reaction Cold
Ammonia 59/59 0.008 0.003
Ni Reaction Cold
Ammonia 60/60 0.029 0.017
Cu Reaction Cold
Ammonia 63/63 0.010 0.012
Table 3. UPW DLs and BECs in ppt measured in Cold Plasma mode.
3. The Purest Water in the World. Jon, Y. 2022. Asianometry.
https://www.asianometry.com/p/the-purest-water-in-theworld#:~:
text=Fabs%20use%20ultrapure%20water%20
to%20rinse%20wafer%20surfaces%2C,water%20each%20
minute%2C%202-3%20million%20gallons%20each%20day.
4. Characterization of Ultrapure Water Using NexION 5000
ICP-MS. PerkinElmer. 2020. Waltham, MA.
Brought to you by
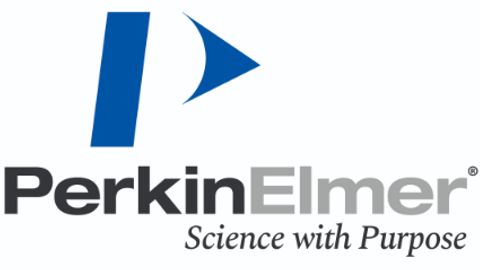
Download the Whitepaper for FREE Now!
Information you provide will be shared with the sponsors for this content. Technology Networks or its sponsors may contact you to offer you content or products based on your interest in this topic. You may opt-out at any time.
Experiencing issues viewing the form? Click here to access an alternate version