Transforming the Semiconductor Industry With Advanced Analytics and Sustainability
To surmount challenges and maintain its growth trajectory, the semiconductor industry must continue to innovate
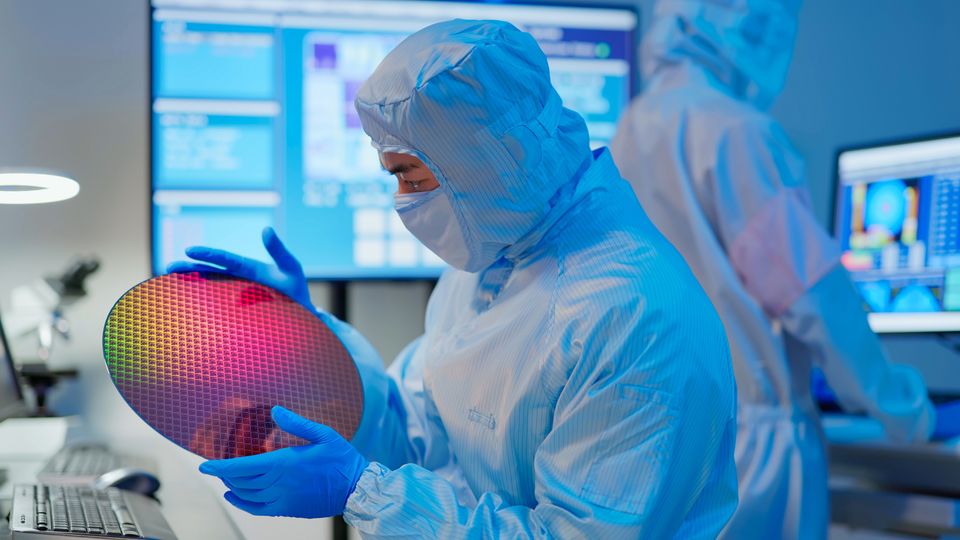
Complete the form below to unlock access to ALL audio articles.
Semiconductor industry trends and insights
Despite seasonal fluctuations and macroenvironmental uncertainties, the semiconductor industry has shown resilience in 2025 following a significant rebound in 2024 largely due to a boom in AI applications. Global semiconductors sales are currently expected to reach $1 trillion by 2030, with demand being driven by technological innovations, including continued interest in generative AI, the growing use of digital twins and advances in autonomous driving technology. The explosive growth in data traffic and generation is also driving demand for additional computing power.
To surmount these challenges and maintain its growth trajectory, the semiconductor industry must continue to innovate. By leveraging new technologies, such as advanced analytical tools, it can strengthen its ability to respond to shifting market needs and drive progress.
Challenges and opportunities
There are several critical challenges facing the semiconductor industry, including yield loss and pressure to enhance its sustainability. Fortunately, advanced analytical instruments can play a crucial role in overcoming these hurdles by providing precise impurity testing and improved quality control (QC), which are essential for reducing failure rates and enhancing overall manufacturing efficiency.
Yield is the key to the competitiveness of semiconductor factories (fabs), directly influencing cost and production capacity utilization. With around 50% of yield losses caused by contamination,1, 2 yield enhancement and contamination control are key priorities for manufacturers. However, this can be demanding as contaminants can enter the manufacturing process at a number of stages, including implantation, etching, deposition, planarization, cleaning and lithography.
Also, due to line widths getting smaller and film layers getting thinner (down to 10 nanometers), the impurity content has to be maintained down to parts per billion in order to ensure consistent yields from integrated circuit (IC) fabrication. As even ultra-trace contaminants can decrease yield and impact product reliability, impurity analysis must cover all stages of the manufacturing process, from ultrapure water and wafer fab materials to quality assurance (QA) of the final product and even the contaminants from the cleanroom air and fab equipment.
QC for wafer fab materials (e.g. wafer, processing chemicals, photoresist, electronic specialty gases, sputtering target materials, etc.) is vital. It is therefore essential to maintain optimum QA/QC, using established standardized testing and inspection procedures, at each stage of the supply chain as this can mitigate contamination, materials variability and formulation discrepancies.
The conflict between chip manufacturing and environmental protection is becoming increasingly prominent due to the continued expansion of global semiconductor production capacity. To address this, companies are developing environmental, social and governance (ESG) guidelines and policies that support green manufacturing, green design, green procurement and green products. Sustainable chemical management – a proactive approach to handling chemicals that prioritizes human health and environmental protection – is another key component of a successful ESG policy as it emphasizes transparency, collaboration and continuous improvement in chemical management practices.
Examples of this shift is the study of alternatives for per- and polyfluoroalkyl substances (PFAS) and PFAS abatement. Materials containing PFAS are critical in semiconductor manufacturing as they offer a unique set of properties, including surface tension, stability and chemical compatibility, that many semiconductor applications require. These compounds are used in processing chemicals and manufacturing equipment, ensuring reliability and performance. However, PFAS pose significant environmental and health challenges. The semiconductor industry has been identifying, testing and implementing improved process controls to minimize the release of hazardous substances into the environment, including PFAS-containing materials.
Technologies helping the semiconductor industry address challenges
The advent of new technologies is empowering the semiconductor sector to tackle existing challenges and seize new growth opportunities. Forming partnerships and fostering collaborations are crucial for advancing innovative technologies and enhancing service capabilities throughout the entire semiconductor value chain. This encompasses areas such as process monitoring, QC of wafer fab materials, detection of inorganic and organic impurities, identification of nanoparticles, adherence to environmental health and safety standards and vacuum leak detection.
The development of impurity testing and QC techniques has been mission-critical for maintaining high yield rates and reducing processing costs. The most troublesome contaminants are metal impurities and particles, which may cause component leakage, reduce the breakdown voltage of components and potentially cause malfunctions and failures.
Advanced techniques, such as inductively coupled plasma-mass spectrometry (ICP-MS), are indispensable for detecting trace and ultra-trace elemental impurities and particles at each stage of the manufacturing process. Inductively coupled plasma-optical emission spectroscopy (ICP-OES) is also suitable for high matrix materials testing used in IC manufacturing.
Besides elemental impurities, monitoring and controlling organic contamination throughout the manufacturing process is critical, as even trace-level impurities can reduce yields.
The semiconductor industry faces QC challenges with raw materials, and a range of substances including photoresists and chemical mechanical planarization (CMP) materials. These challenges include research to improve production quality, and tasks such as analyzing polymer molecular weight, controlling synthesis processes, conducting formulation research, identifying impurities and purifying chemicals. The difficulty lies in a lack of available data.
One strategy is to leverage multi-platform testing techniques, such as gel permeation chromatography (GPC), high-performance liquid chromatography (HPLC), liquid chromatography-triple quadrupole mass spectrometry (LC-QQQ), liquid chromatography-quadrupole time-of-flight (LC-QTOF), gas chromatography (GC) and gas chromatography-mass spectrometry (GC-MS). Together, these can gather the comprehensive data required to ensure that products comply with the strictest requirements.
For cost-efficient manufacturing, automated and intelligent solutions, such as online/inline monitoring of contaminants in water, process chemicals and the environment, help ensure that every stage of the manufacturing process, from the wafer fab materials to wafer testing and final product QA, meets the highest standards. This helps improve root cause analysis and speeds up yield improvements.
Analyzing the optical properties of semiconductor materials is also critical. For this, ultraviolet/visible (UV/Vis) spectroscopy is used to test the transmission, scattering and reflection of film-coated wafers in devices such as CPUs and RAM. This helps evaluate the optical performance of coating layers and checks their uniformity. The results can help identify and address any issues in the coating process.
In addition to supporting manufacturing and improving purity and yields, advanced analytical tools also support regulatory compliance. The semiconductor and electronics industry must comply with a range of environmental health and safety (EH&S) regulations and industry standards, such as registration, evaluation, authorization and restriction of chemicals (REACH), restriction of the use of certain hazardous substances in electrical and electronic equipment (RoHS), waste from electrical and electronic equipment (WEEE) and SEMI. These govern processes from raw materials testing to QA/QC of final products, ancillary processes, such as emissions monitoring and control, as well as wastewater discharges.
For example, addressing PFAS challenges requires substantial investment in research and development to find viable alternatives that match their performance and stability, while complying with regulations to reduce PFAS emissions and ensure safe handling and disposal.
Advanced analytical tools are crucial in this effort, enabling precise monitoring of PFAS levels in manufacturing facilities, materials and the environment. These tools help manufacturers detect and mitigate PFAS emissions, ensuring compliance with stringent environmental regulations.
The future of the semiconductor industry
The semiconductor industry is on the brink of transformative growth, driven by a range of demanding technological developments. It is simultaneously faced with calls for heightened sustainability from both regulators and customers. Balancing these twin demands, while also maintaining productivity, is a challenge. Fortunately, the use of the latest testing and QC techniques is already helping fabs deliver the next generation of high-performance products, and improve their yield, while strengthening the industry’s environmental credentials.
References
- Pan TM, Ko FH, Chao TS, Chen CC, Chang-Liao KS. Effects of metallic contaminants on the electrical characteristics of ultrathin gate oxides. Electrochem Solid-State Lett. 2005;8(8):G201. doi:10.1149/1.1945367
- Handbook of Silicon Wafer Cleaning Technology. Eds Reinhardt KA, Werner Kern W. 3rd ed. Elsevier; 2018. doi:10.1016/C2016-0-01001-X